Chiński Seres pochwalił się wielką magnezową maszyną odlewniczą, która może zacząć masowo produkować części do samochodów elektrycznych. Firma we współpracy z Huawei wytwarza auta pod marką Aito, dlatego wkrótce mogą one stać się lżejsze i zyskać większe zasięgi bez konieczności modernizowania baterii. Auta z częściami z magnezu powinny być też mniej (acz wystarczająco) sztywne i powinny okazać się tańsze w produkcji.
Magnez, kolejny kierunek optymalizacji?
Samochody elektryczne wymusiły przyspieszenie prac nad optymalizacją podzespołów stosowanych przez branżę motoryzacyjną. Ciężka bateria powoduje, że z dotychczasowych struktur aut, które jawiły się jako „wystarczająco dobre”, konieczne było urwanie paruset kilogramów. Na początku 2025 roku najlepiej radzi z tym sobie Tesla, której elektryki są coraz bliżej odpowiadających im modeli spalinowych (Tesla Model 3 RWD = 1,76 tony, VW Passat 2.0 TSI = 1,66 tony, BMW 318i = 1,58 tony).
Chińczycy od kilku lat mocno eksperymentują z magnezem. Są największym na świecie producentem tego metalu, spodziewają się, że użycie go może obniżyć koszty produkcji aut elektrycznych przy okazji dając im wyższe zasięgi. Magnez jest podobny do aluminium, ale jest od niego lżejszy o około 30 procent, lepiej też tłumi wstrząsy (mniejsza sztywność). Jednak jego najistotniejszą cechą jest wyższa wytrzymałość w stosunku do masy – magnez przydaje się wszędzie tam, gdzie obniżanie wagi stanowi priorytet.
Kilka miesięcy temu chińscy naukowcy pochwalili się, że opracowali maszynę odlewniczą potrafiącą produkować felgi ze stopów magnezu. Użycie lżejszego pierwiastka pozwoliło na obniżenie wagi każdej z felg o 7 kilogramów w stosunku do stopów glinu (Al). W trakcie salonu samochodowego Auto Shanghai 2025 Seres ujawnił, że dysponuje maszyną odlewniczą zdolną do masowej produkcji części tylnego podwozia. Wytwarzane przez nią odlewy są lżejsze o 21,8 procent w stosunku do aluminiowych.
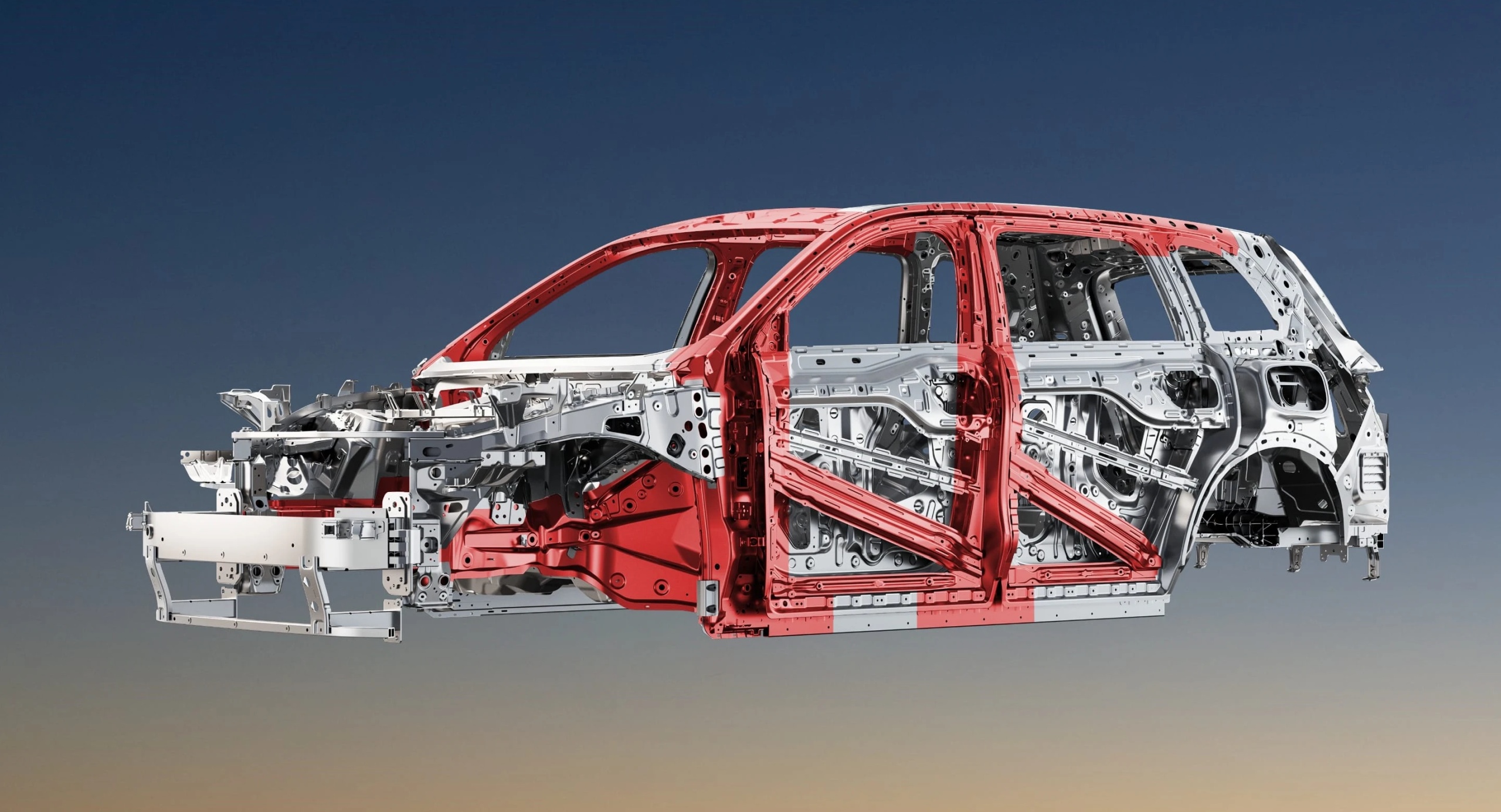
Struktura Aito M8. Na czerwono zostały zaznaczone elementy z ultrawytrzymałej stali. Zdjęcie ilustracyjne (c) Aito
Przedstawiciel Aito przyznał się, że w samochodach marki stosowane jest „ponad 10 części” wykonanych z magnezu ważących około 20 kilogramów. Duży odlew w tylnej części podwozia to tylko jedna część (plus mocowania), której zastosowanie może przynieść zbliżone oszczędności na wadze – jest więc o co walczyć. Trzeba wszak zaznaczyć, że pierwiastek nie trafił jeszcze na większą skalę do masowo produkowanych modeli, nie wiadomo też, czy będzie stosowany przez Seresa w pozycjonowanych wysoko samochodach Aito, czy może zejdzie niżej, do rodzimej marki producenta.